Interviewed by Sille Pihlak
There is an ongoing discussion how to reach novelty in architecture with computation-driven tools, combining material knowledge with fabrication possibilities. In an attempt to seek for the new spatial qualities emerging and deepening the collaboration between the stakeholders of construction, we discuss it with experimental architect Rachel Armstrong, fiery engineer Manja van de Worp and innovating fabricator Jelle Feringa. All interviewees have recently visited the Estonian Academy of Arts to hold a public lecture.
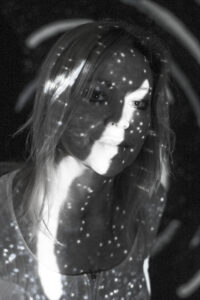
Rachel Armstrong is a Professor of Experimental Architecture at Newcastle University and an internationally acclaimed academic and pioneer in innovating environmental solutions and interdisciplinary practice. She designs and engineers architectural applications in the built environment, which are based on the properties of life-like chemical and biological systems.
NOVELTY
What does the term “Experimental Architecture” mean for you and where does it become non-experimental?
Experimental architecture is an approach to design arising from visionary practices, which provoke alternative narratives for architectural subjects. Experimental architecture developed during the late industrial age during a period of techno-optimism, where disenchanted by existing modes of urbanisation, it used the cutting-edge industrial developments to increase people’s freedoms with walking buildings and plug-in cities. Originating from visionary practices that provoke alternative narratives for architectural subjects, the drawing board became a laboratory which could change the very nature of architecture. While experimental architecture’s agendas have mostly been forged through the collaboration with emerging industrial technologies, such increasingly ‘smart’ machines have also shown their dark side. We are facing a crisis where high-tech computers that run our present neoliberal society are exacerbating global inequalities and their emissions contribute to disruptive weather events. The cutting-edge technologies upon which experimental architecture based its vision of the future are therefore creating the antithesis of its ethos.
Experimental architecture is an inherently transdisciplinary, self-critical and reflexive form of design-led research practice that explores ideological and practical counterpoints, which value pedagogy and prototypes over formal objects. It shifts the boundaries between subjects to provide a platform where the drawing board becomes a laboratory that through an engagement with new materials, technologies, ‘monstering’ and prototyping methods can change the consequences of making a building. While it decentres established modern/industrial tropes, experimental architecture does not reduce the status of human agendas. The transdisciplinary nature of experimental architecture is not fixed or bound to a specific intellectual trajectory but evolves through research trajectories, as discussed through the practice of ‘monstering’.
In an ecological era, the scale of our challenges exceeds the human and stretches out into the cosmos and down into the subatomic scale. In exploring these terrains that are too big for our senses to fully comprehend, the ecological experimental architects engage with a practice of ‘worlding’ that exceeds the conventions of traditional architecture in ways that are pertinent to 21st century challenges. In this way experimental architecture never loses its critical and immersive approach to knowledge, yet it produces working prototypes of ideas such as the living brick for the Living Architecture project, which has received €3.2m funding from the European Union’s Horizon 2020 Research and Innovation Programme and is a collaboration of experts from the several European universities. This is a project that very realistically explores how different units of construction that support different metabolisms (aerobic, anaerobic and synthetic) can be coupled together to alter the impacts of a building on the environment. It has already made a product that is about to enter the market – Doulix – which is a synthetic biology toolkit made by Explora. Experimental architecture prioritises catalysing appropriate change within the practice of the built environment.
Materiality
You have been listed in Wired magazine Smart List 20131 as a sustainability innovator. Where does material stand in your work process and from where do you depart in your designs?
Sustainability is an interesting term as it proposes to broadly maintain the benefits of the status quo while being more considerate about how you go about this. At a time of change such terminology needs to be replaced by notions of adaptation or evolution. In that sense the material developments and technologies that I have explored have also evolved and changed with time. I started out exploring ways to literally confer buildings with the properties of life so that they could engage in a ‘natural struggle for survival against the elements’.
The first materials I used were protocells which are analogue autonomous agents that can be chemically programmed. It is astonishing how lifelike they are and that they do not need a central control system to govern their behaviour. They were positioned as a responsive material that could react to changes in the building foundations in Venice, forming protective ‘biocrete’ around the woodpiles as they were exposed to the air by changing water levels. Considering the process of metabolism, protocells could potentially work with the biofouling around the shores of Venice so bioconcretes could be strategically built up around damaged sites.
However, working with protocells was tricky as they are not complex as living organisms, so I looked to diversify the range of agents that would potentially confer lifelike properties upon building materials. The living architecture project aims at developing more sophisticated and programmable ‘living bricks’ than possible with protocells by harnessing the metabolisms of microorganisms. The brick consists of a structural material like ceramic, glass or concrete and it also has interior chambers and details that can harvest specific properties from these modules. The living architecture project uses three different kinds of metabolism (anaerobic, aerobic and synthetic) to produce a range of substances within the structure of a building. While the current project is high-risk and experimental, it helps to develop a more strategic use of water in our living spaces, setting the scene for water recycling and purification within homes, where houses have circulations and ‘architectural’ kidneys (like sewage processers) rather than drains.
How has the position of material changed throughout the history of architecture and what is it today? Does it have enough input to geometry, construction and to the overall concept?
The main change I would argue is that historically we have looked for permanence in architecture and used inert materials at equilibrium states which change very little with time. In an age of uncertainty and chaos, materials at non-equilibrium states become interesting as they possess their own energy and agency. This means these materials are capable of making ‘decisions’ based on the state of their environment through analogue strategies. These changes may be as simple as materials that absorb water and change shape such as Achim Menges HygroSkin and Skylar Tibbits 4D printing. Rather than having a ‘dead’ building that is unresponsive to its surroundings, these new materials enable our living spaces themselves to adapt to pertinent changes.
Why do we need to discuss sustainability and material optimization as architects? Where do you see it could lead our profession?
We need to discuss these options as contemporary architecture has a negative impact on our environment. Currently it is responsible for 40% of our total carbon emissions. Given that our cities are the largest built structures on the planet, small changes in the way that buildings are made and perform could radically alter our collective impact on the natural world. Should we get this relationship between taking from the planet, responding to it and giving back to it right, then perhaps the solution to healing a stressed ecosystem and the people who are part of it would be to create a building.
Applicability, fabrication, production
What could we take from the academic environment and bring to professional setting already today, regarding construction methods, ways of creating space, non-standard materials?
For me the question is: when is it appropriate for academics and industry practitioners to work together? Not everyone wants change. In my experience such collaboration works best when there is a mutual need for and investment in change. When parties want to expand their worldview and take risks that lead them towards new knowledge and a greater portfolio of tools for working in alternative ways, then this sets the scene for highly productive partnerships. The important aspect is that all stakeholders contribute something and share the overall risk in the collaboration. But it is hard and sustained work, not a panacea, it is not for everyone.
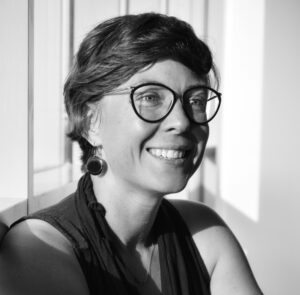
Manja van de Worp launched NOUS engineering LONDON (now YIP) in 2013, an engineering consultancy bearing extensive knowledge of advanced structural analysis tools, complex structural systems, materials and fabrication technologies. Current projects focus on structural product design and research-based projects, looking at innovative ways to use timber, 3D printing of concrete, searching how materials not conventionally used in structural design could find their way into building engineering.
Novelty
What does the term “Experimental Engineering” mean for you and where does it become non-experimental?
“Experimental Engineering” in our office NOUS engineering / YIP London means exploring new hybrid typologies of structural behaviour which are not yet named, i.e. new relationships between structure, material, geometry and fabrication. These new behaviours allow us to create different links between integrated architectural form and structural form performance. The non-optimized, in contrast to searching for that one data-driven outcome, allows for a needed room of “error” that can become a new strategy / design methodology. It is that non-tunnel-vision that allows these new structural possibilities to arise. An experiment already states there is a hypothesis, a dream constructed by near enough facts that is to be tested. The non-experimental could be read as purely resolving the structure, as opposed to trying to enhance the performance, which the experimental approach offers.
Having said that, to me all projects are experiments, where I am to find new links between architecture and structural design. What if we could ….? For example, design a lintel like a waterfall, shedding loads through the wall instead of one beam doing everything, removing the heavy line above the window (B-de-C, London 2012) or using the prestressing capabilities of dried seaweed to prestress aluminium and bamboo structures (Oki Naganode, London 2013).
Are some designs sometimes too rational and current for you?
Perhaps it has nothing to do with pure rational or current nature of design, but maybe the method of mountain-valley-effect should be removed from the equation in its way of thinking and we should provoke a more integrated holistic design process. By the mountain-valley-effect I mean, if there is too much of one thing, “sun” provide a solution “shading”. True, but this can be done with blinds, in a way an isolated solution, compared to the example of Sanaa New Art Museum in New York, of an integral approach whereby generating an overhanging between parts of the building self-shading occurs, but spaces are well-lit differently and balconies are created. So, light can form the basis of the design but it can also be subtly tackled in the background. I like the idea to always consider 1+1 = 3, where together with providing the shading we explore other possibilities.
Materiality
You are a truly material-driven engineer, often jumping between the digital and the physical. Don’t you have trust in programs and data?
I get inspired by materials and their possibilities in terms of performance through fabrication and geometry. There is a certain freedom when physically experimenting with materials, something that is not pre-set. Data and analysis software driven design are essential to prove new structural design and I do trust the software. But when doing something less conventional, the physical performance captured could not be assumed as easy in the computer, as it requires a simulation of the behaviour, this can only be done when we have a certain understanding and “feel”, i.e. the more intuitive side of a design process.
This is often misunderstood, as it seems nowadays digital design equals complexity or automatically inventive new designs. Which is not true. Whenever an input is generated, an output will be produced, but we do not know if our assumptions for simulation have been set correctly when experimenting outside the standard boundaries. Through experimenting in both the digital and physical world, we can get a different “feel” for a certain structural behaviour and possible application – but typically for both methods a very different one – when they can inform one another. I work with both simultaneously and move seamlessly between them. The beams designed by structural engineer Robert Le Ricolais (1970s) do not just roll out of a software, but the concept generated can be extrapolated upon using digital design.
How has the position of material changed throughout the history of engineering and what is its role today?
Material has always been important in developing new structural systems. The key is the combination of new mechanical material properties affecting strength and stiffness through fabrication or construction. Pressing metal sheets allowed form and material to be merged and increase structural possibilities, 3D printable rapid-setting materials and the method of construction created the new possibility to rethink part & whole in construction. It is not material in its own or in combination with fabrication, it is also simulation of the unknown behaviour that changed its application and position in creating new possibilities in design. Form finding with materials in structural design has been and still is essential, but now we are able to hybridise and expand on a simple idea because of the simulation tools available.
Why do we need to discuss sustainability and material optimization?
Longevity and the impact of time to design are important. Here sustainability is not only about optimisation or economic use of resources. It can also be the reuse or disassembly of materials or the kit-of-parts of a design. These “kit-of-parts” concepts can be found at the scale of Kurukawa’s Nakagin tower, or the A-frame in Prouve’s house, or a building block – almost acting like Lego as in the structure we designed with Gilles Retsin for the TAB pavilion 2017. For me the more sustainable form of optimization is to house multiple performances, to be able to adapt over time, so perhaps actually not optimized but more versatile. My ongoing research for 10 years has dealth with this idea of embedded performance, multiple stable states, a continuous equilibrium.
Applicability, fabrication, production
What could we take from the academic environment and bring to the professional setting already today and could the long-term potential be taken over?
We can take a place that is free from boundaries which explored facets between different industries and beyond the boundaries of disciplines. For example, in terms of open source design and digital fabrication techniques, bridging textile industries and the idea of the custom Nike shoe could easily find their way into architectural CAD CAM fabricated façade panels or mass-customised fabric formwork solutions for the concrete industry. It also allows for different facilities in practice or academia in terms of fabrication or recourses to be mixed. Here prototyping can be done both physically and digitally.
Where do you see the biggest thresholds regarding methods (communication and tooling) in the field of construction and how could this be solved?
The main threshold, obstacle, in our current industries is the loss of the idea of the master builder, who would bring all aspects of design together. This is very different from acting purely as a consultant. A more integrated approach and cross-fertilization between disciplines allows to be free and to explore and exploit knowledge between fields. The question now arises what should the trade of this new master builder be: Is it the architect? Or a new professional? Is the new master builder a hybrid of a digitalised team of thinkers? I think in the latter lies the possibility for a new field of collaborative design to be explored.
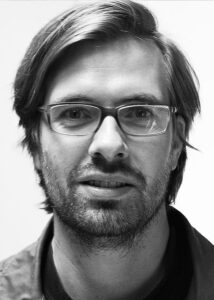
Jelle Feringa is a co-founder of EZCT Architecture & Design Research and for the last few years he has been working on projects that try to harness the full potential of robots in architecture. In 2012, the Danish architectural robotics company Odico was founded on the basis of Jelle’s PhD research. Since early 2017, Jelle is CTO at Aectual in Amsterdam, where robotic manufacturing and product development is vertically integrated.
Novelty
What does the term “Experimental Architecture” mean for you and where does it become non-experimental?
The collection of the FRAC Centre, Orléans has had an impact on my understanding of experimental architecture. The catalogue “Architectures Expérimentales 1950-2012” is a wonderful reference and I think of the FRAC’s collection as a collection that precisely addresses this question “What is experimental architecture?”. By bringing about the ArchiLab events, the FRAC has had an important supportive role in the development of experimental architecture for the past two decades.
I think of the field of architecture as inclusive, all encompassing, about building a world view and the discipline of architecture as an exclusive force. While EZCT took place in the field of architecture, Odico, Aectual are rooted in the discipline of the field. When you move from a research practice to a building practice, you transition from the field of architecture to the discipline of architecture.
The best experimental architecture takes place right at the border of these domains. Building is all about mitigating risk, hence there is so little room for experiments to take place. Architecture is synonymous with experiment in advancing the discipline. When there’s no experiment, your architecture has dissolved and you are merely building.
Why do we need to discuss the potential spatial changes that working with robotics could bring to architecture and what could they be?
I’m not sure whether spatial changes are the key drivers advancing the field. What’s depressing about architecture is its contribution to pauperdom, since as an architect you often design or realize a project that’s beyond what you could afford yourself. That’s what I find striking about Modernism – its economic agenda. For Ledoux, economy and aesthetics are one and the same. “It is for the architect to oversee the principle, he can activate the resources of industry, husband its products and avoid costly upkeep, he can augment the treasury by means of the prodigal devices of art”. Architecture is a function of Capital, you are trying to maximize the means entrusted to you. It’s no different from Ghiberti and Brunelleschi trial pieces for the Florence baptistery doors. It is claimed that the patrons of Florence were interested in an artist who would also maximize the disposable resources of bronze.
On a similar note, when you see the effortlessness of the Truffle project of Ensemble Studio in contrast to the considerable effort that the woven carbon pavilion of ICD/ITKE Research Pavilion must have taken, it does highlight that the issue of a master of automation is still an open question. I consider myself a technologist, but it is important to have an encompassing idea about what constitutes technology. Ensemble Studio’s approach is a dead-pan kind of approach but ultimately a technological one as well.
Charles Eames’ maxim “the best for the most for the least” is a key driver for me, trying to think of aspects of economy in the broadest sense. With my students at RC101, we’re revisiting Thomas Edison’s idea of the single-pour house. “Deadpan” is an undervalued idea in architecture. As Frei Otto suggested, “The secret, I think, of the future is not doing too much. All architects have the tendency to do too much”.
Do you consider the general field of construction too rational and short-sighted?
I recall a student when I lectured at the Estonian Academy of Arts last year, who introduced himself as a blacksmith. I find the nostalgia revolving craft a dangerous and unethical kind of nostalgia. When you think of it, it truly is the inversion of Eames’ aphorism “the worst for the least for the most”. That said, I’m nostalgic for the optimism and vitality of the Modern era, and the incredible productivity of industrial robotics hence is a umbilical cord of that era perhaps.
Lincoln hinted at the absurdity of acting rational, “Give me six hours to chop down a tree and I will spend the first four sharpening the axe”. If someone time-travelled from the Medieval ages, our construction sites would be a relatively familiar territory to such a person, but some understanding of the nuclear fusion project ITER would be so far beyond their comprehension, such a splendid power would shake their beliefs. Which is ironic since the medieval masons clearly were the technologists of their age. Let not forget that Brunelleschi was the Elon Musk of his day.
Materiality
Where does material stand in your work and how does it influence your design and work process?
I’ve had the fortune to have been an artist in residence at the Van Doesburg house, in Meudon, a suburb near Paris. The house was built out of bales of compressed hay, which was a novel and innovative material. There’s something noble about making the most from modest materials. Perhaps my long-time fascination with the compressed hay bales of our time, EPS foam, stems from living at Van Doesburg house. I love concrete and foam, materials for which there is no alternative. I’ve explored diamond wire cutting of large marble blocks. It’s almost a primordial need for an architect to conquer working in natural stone. Perhaps a nostalgia to the masonic origins of the profession.
Why do we need to discuss sustainability and material optimization in the field of construction? Where do you see it could lead architecture?
Annually, 3.82 billion cubic meters of concrete is produced, that’s about 8,786 billion ton of material. The world population is approximately 7.3 billion, so 8,786 divided by 7.3 equals a consumption of roughly 1.2 ton per person per year. There is no real alternative to concrete, I guess that concrete cements the anthropocene. The development of materials such as aerated or insulating concrete with glass foam is an important development. As a building material, EPS foam has similar unrivalled qualities. With Asbjørn Søndergaard, I developed a pavilion where we’ve explored robotic hotwire cutting and topology optimization, but in terms of effectiveness there’s a lot to be gained from the development of composite cementitious materials.
Applicability, fabrication, production
How applicable is academic research in today’s construction scene? Is blue-sky research too far and distant or should academia deal only with future topics and advanced fabrication methods? In maths, academia is the impetus. In physics, it is similar but less absolute. In architecture, where pragmatism rules, practice is more of an impelling force than academia. But true deviations, true innovations rarely come from the academia in terms of construction, but they certainly do in terms of architecture. But again, coming back to fundamental research in energy or physics, thinking of the particle accelerators or the ITER project in France, where these projects take thousands of scientists to develop and about half a century to complete, in that light there’s no such thing as blue-sky research. The upside of this is that some 25-year-old second-hand robots can buy you leverage in architecture at a very low cost. The problem in our field is that spill over from research to the establishing of new practices, such as I’ve been so lucky to achieve with Odico and Aectual, and EZCT co-founder Philippe Morel with XtreeE, is all too rare. In order to have impact you need to deliver real projects. In academia, our deliverable is a scientific paper, which works for maths and physics but has a modest impact in architecture. A house as a PhD is a defensible idea, I think.
What could we take from the academic environment and bring to professional setting already today, regarding construction methods, ways of creating space, non-standard materials?
JF: It’s not very modest, but my academic work in robotic hotwire cutting and diamond wire cutting has led to industrial uptake and it’s too rare that academic work is further developed in practice. This has everything to do with Pareto’s law, 80% of the work is done in 20% of the time. Achieving industrial readiness of technology is time intensive and is a true mismatch with the “publish or perish” dogma in academia.
Where do you see the biggest problems and missing outs regarding methods (e.g. communication, tooling, will to experiment) in the field of construction and how could this be solved?
We’re still lightyears away from the “lights out” mode of operation of automotive factories. This is very much on my mind in my work in developing 3D printing strategies in Aectual.
HEADER photo by Rachel Armstrong. Self-assembling chemical structures, prototypes for the “Hylozoic Ground” installation.
PUBLISHED in Maja’s 2018 spring edition (No 93).
1 http://www.wired.co.uk/article/the-smart-list-2013